Industry 4.0 and the pursuit of resiliency
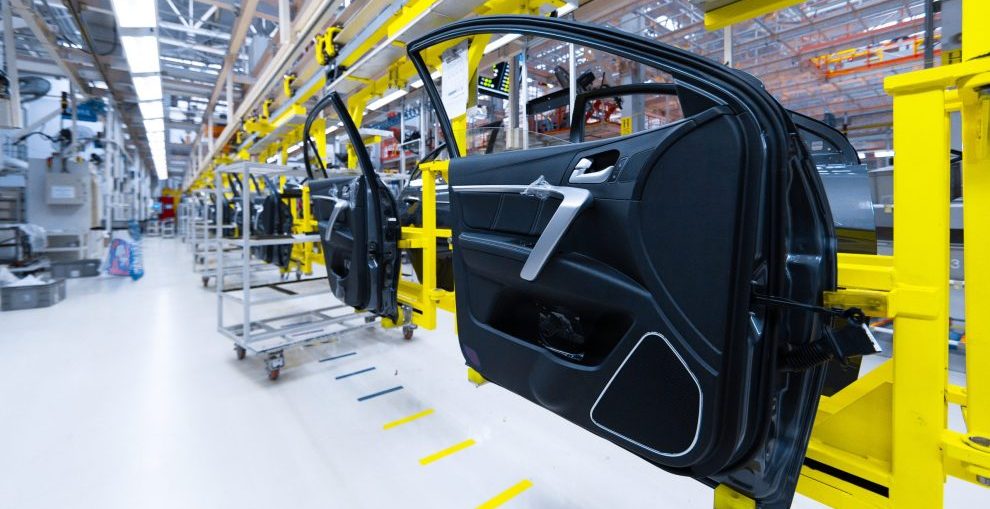
Downtime can cost a manufacturer upwards of USD 21,000 per minute. Fortunately, AI has evolved to accurately identify issues and take action. This advanced technology allows companies to easily add intelligent “eyes” to their operations with standard mobile devices — the same smartphones and tablets that you’re using right now. All to quickly identify defects in production outputs as well as remotely monitor assets for potential disruptions.
I talked with IBM expert Scott Campbell about this AI evolution and his current focus: helping clients intelligently manage their assets with Zero D, which stands for zero defects and zero downtime. Scott has had numerous product management roles within IBM. And almost all of them centered around some type of AI technology. First in financial environments, then with Red Bull racing (where his team used AI simulation to understand race dynamics), and now as the lead product manager for IBM Maximo and IBM TRIRIGA.
What’s the biggest challenge manufacturers face right now?
Every manufacturer knows that there’s a tremendous value if you can eliminate defects and stop rework. If you can keep your manufacturing facility running 24×7 without any downtime, it’s almost a given that there is ROI there. The challenge is how do you actually transition from a reactive environment — which is where most manufacturers are — to a proactive environment. So instead of thinking, we have a problem to fix, how do you think instead, we’re anticipating problems to fix before they actually become problems. The cool thing is, IBM has AI technology that is sophisticated enough to let a company do that effectively. But we have to make sure that it’s trustworthy. When a company looks at all this data, they have to believe in it. Otherwise they’ll go right back to reactive maintenance.
A lot of people talk about Industry 4.0, but I think the big challenge for many manufacturers is how do you even get started? How do you take something that’s transformational and evolve it over time? Because you can’t do this in a big bang approach, or a forklift upgrade approach. You have to evolve it. And you have to start somewhere.
Starting with defect detection is a good way to get introduced into an AI environment that’s fairly easy to understand. It’s pictures, it’s images. You can see the system is doing a better job than an individual can do, and that makes it easier to expand use of that technology. Once you begin to build trust in those results, it’s easier to use machine learning and AI technology for maintaining the assets running on the manufacturing floor. Then you understand the health of an asset, you know hey the odds are really high — a probability of 85 to at 95% — that this asset is going to fail sometime in the next 45 days, so let’s do something about it.
And manufacturers are moving toward this?
Oh, yeah, you’re seeing it across the board. There’s a big North American auto manufacturer using AI visual detection and predictive monitoring, and they saw immediate results. It’s incredible how quickly they were successful just running a simple pilot. They found 30 defects in the first 30 days, which isn’t that big of a deal. But they were looking at one single connector in one point of their installation, tied to one specific problem for them. When they expanded that to multiple locations on their assembly line, they found up to 200 defects a day. So in the very first month they gained a USD 1.8 million savings on that one manufacturing line.
There are two parts to the Zero D story. Visual inspection and asset performance management (APM). Visual inspection uses computer vision models focused on quality inspection. APM uses machine learning models based on time series data to determine health of assets and probable failures in the future. Toyota is using Maximo Visual Inspection, and now they are also using the Maximo Asset Performance Management (APM) suite. They tested Maximo APM on some of their machinery that does liquid cooling and found that was another problem area for them. By implementing the software into this pilot, they are now able to monitor the asset health 24×7 and predict probability of failure in the future. It is the foundation for them to shift from being reactive and cycle-based, to practicing a proactive, reliability-centered maintenance strategy. This will be transformational for their entire organization.
Those are just two examples of where Industry 4.0 and how intelligent asset management has started to gain traction. Of course, there are lots of others, but those two examples are true showcases for transformational manufacturing processes.
Does adopting Industry 4.0 bear out all the way down the line to the customer?
Yes, it does, especially on two fronts: quality and meeting demand. For Toyota, quality is mission one. Fewer recalls and less warranty work (compared to other vehicle brands) drives customer loyalty, not to mention reduced costs for rework.
Then when it comes to meeting demand, it’s estimated that downtime costs on average about USD 21,000 per minute. That means within an hour, you have a million-dollar problem. And if you can’t meet the demand, somebody else will. There’s loyalty in car buying, but there is also availability, especially with the chip shortage.
When it comes to defects and downtime each topic seems big enough on its own. Why not tackle them separately? Why do you advocate handling them both at once?
Either one of them is critical. But you achieve true transformation when you attack them both at the same time. Because no matter how high your quality is, you can’t meet demand if you have downtime. Conversely, even if you’re super effective in your manufacturing processes but your quality inspection is poor, you’re just adding to your scrap heap or your rework at a tremendous pace.
That’s why it’s the combination of AI-based visual inspection for quality and asset performance management for predictive repair that lets you increase quality and production efficiency at the same time — and that helps build a sustainable and resilient business.
Do you have any other hard numbers around the savings that an intelligent asset management program could bring to a manufacturer?
Of course, this approach is applicable beyond the auto industry. It’s just a very good use case that folks understand. If you look at the rework of a defect — and it’s important to distinguish between a defect and rework — a defect can occur in the production line, but it only becomes rework if it goes undetected through final production. If you catch it, and fix it, before it gets to the next stage of the line, it’s no longer a defect. We emphasize detecting and correcting at the point of installation.
If a defect turns into rework work — which means if it’s either caught in final inspection or somewhere down the line, even potentially by the customer — then it’s about USD 300 per incident. So, if you think of that North American auto manufacturer who found 200 defects a day, they saved USD 300 multiplied by 200 defects multiplied by 365 days. That’s how you hit very large numbers very quickly in terms of saving.
Can you also talk about the savings from not over-maintaining an asset and only performing maintenance when it’s actually needed?
When our customers understand “$21,000 a minute,” they tend to create very rigid maintenance schedules. The problem is they have no knowledge of what actually needs to be fixed. It becomes hey we’re going to check everything once a week. There’s the idea that frequent maintenance schedules are cheaper even though it’s overkill.
But with an APM platform, you can reduce your maintenance and improve uptime — all at the same time! It is prescriptive in terms of understanding where you need to actually apply resources. It provides 24×7 monitoring of the health of assets, can detect anomalies before they become critical issues, and can predict the probability of failure in the future. Technicians are no longer tied to calendar-based scheduling. Because now a company has the data that indicates these assets are just fine and they’re not going to fail for another month, several months, or even years. This means technicians, who are becoming a scarce resource, can better schedule their time. And companies can utilize technicians much more effectively in the areas that have the highest value, based on data they can trust.